Нержавіюча сталь - це металевий матеріал, який порівняно складно машини. Існує дві основні проблеми в обробці обробки: ① Штабна сталь має високу міцність на високу температуру та сильну тенденцію для затвердіння роботи, що легко носити та зменшити термін служби інструменту. ② Швидка сталь має високу міцність, чіпси легко зламати, а також легко пошкодити. Якість обробленої поверхні також є загрозою для безпеки оператора. Тому розрив мікросхем під час повороту також є більш помітною проблемою. У довгостроковій виробничій практиці повороту деталей з нержавіючої сталі було вивчено зовнішній інструмент повороту з нержавіючої сталі
Різна твердість мартенситної нержавіючої сталі після термічної обробки має великий вплив на обробку повороту. У таблиці 1 показана ситуація з поворотом сталі 3CR13 з різною твердістю після термічної обробки з обертовим інструментом, виготовленим з матеріалу YW2. Видно, що хоча твердість відпаленої мартенситної нержавіючої сталі низька, то поворотні показники погані. Це пояснюється тим, що матеріал має велику пластичність і міцність, нерівну структуру, сильну адгезію, і легко виробляти ріжучі краї під час процесу різання, і отримати хорошу якість поверхні непросто. . Після гасіння та загартування матеріал 3CR13 з твердістю нижче HRC30 має кращу трудомість і його легко досягти кращої якості поверхні. Хоча якість поверхні деталей, оброблених, коли твердість більша, ніж HRC30, краще, інструмент легко носити. Тому після того, як матеріал потрапляє на фабрику, спочатку проводиться процес гасіння та загартування, а твердість досягає HRC25-30, а потім проводиться процес різання.
Вибір матеріалів інструментів
Висоткові показники матеріалу інструменту пов'язані з довговічністю та продуктивністю інструменту, а виробництво матеріалу інструменту впливає на виробництво та заточення якості самого інструменту. Тому матеріал інструменту слід вибрати як матеріал інструменту з високою твердістю, хорошою стійкістю до адгезії та міцністю. За тими ж параметрами різання автор провів тест на порівняння на інструментах декількох матеріалів. З таблиці 2 видно, що зовнішній інструмент повороту за допомогою Tic-Ticn-Tin Composite Composite Coating Composite має високу міцність та високу якість поверхні заготовки. Хороша, висока продуктивність. Це пояснюється тим, що лопатки такого роду карбідного матеріалу з покриттям мають кращу міцність і міцність, і тому Токіналізації ЧПУ та перший вибір для зовнішніх інструментів повороту для обробки нержавіючої сталі 3CR13. Оскільки цього матеріалу немає ріжучого леза, тест на порівняння в таблиці 2 показує, що продуктивність різання карбіду, що цементує YW2, також хороша, тому леза матеріалу YW2 може використовуватися як різання леза.
Вибір геометричного кута та структури інструменту
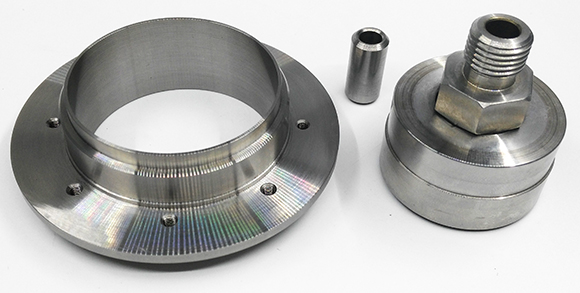
Для хорошого матеріалу інструменту особливо важливо вибрати розумний геометричний кут. Під час обробки нержавіючої сталі геометрію ріжучої частини інструменту, як правило, слід враховувати з вибору кута граблі та кута спини. Вибираючи кут граблі, слід враховувати такі фактори, як профіль флейти, наявність або відсутність камери та позитивний та негативний кут нахилу леза. Незалежно від інструменту, під час обробки нержавіючої сталі необхідно використовувати більший кут граблі. Збільшення кута граблі інструменту може зменшити опір, що виникає під час різання та видалення мікросхеми. Вибір кута зазору не дуже суворий, але він не повинен бути занадто малим. Якщо кут зазору занадто малий, він спричинить серйозне тертя з поверхнею заготовки, погіршуючи шорсткість обробленої поверхні та прискорення зносу інструментів. І через сильне тертя посилюється вплив загартування роботи на поверхню нержавіючої сталі. Кут полегшення інструменту не повинен бути занадто великим. Якщо кут рельєфу занадто великий, кут клину інструменту зменшується, міцність ріжучого краю знижується, а знос інструменту прискорюється. Як правило, кут рельєфу повинен бути належним чином більшим, ніж при обробці звичайної вуглецевої сталі. Як правило, при повороті мартенситної нержавіючої сталі кут граблі G0 інструменту переважно 10 ° -20 °. Кут рельєфу A0 підходить до 5 ° ~ 8 °, а максимум - не більше 10 °.
Крім того, кут нахилу леза LS, негативний кут нахилу леза може захистити наконечник і покращити силу леза. Як правило, G0 вибирається від -10 ° до 30 °. Кут введення КР повинен бути обраний відповідно до форми заготовки, місця обробки та встановлення інструменту. Шорсткість поверхні ріжучого краю повинна бути Ra0,4 ~ 0,2 мкм.
Що стосується структури інструментів, для зовнішніх інструментів повороту використовуються зовнішні точки кругової дуги. Радіус завивки чіпів на кінчику інструменту великий, а радіус завивки чіпів на зовнішньому краю невеликий. Чіпки перетворюються на поверхню, щоб обробляти і розбити, і розрив мікросхеми добре. . Для ріжучого інструменту кут вторинного відхилення можна керувати в межах 1 °, що може покращити умови видалення мікросхеми та продовжити термін служби інструменту.
Розумний вибір суми різання
Кількість різання має більший вплив на якість поверхні заготовки, довговічність інструменту та продуктивність обробки. Теорія різання вважає, що швидкість різання V має найбільший вплив на температуру різання та довговічність руху, а потім подача F та AP найменший. Глибина вирізаного AP визначається розміром заготовки на поверхні, обробленій інструментом на верстаті з ЧПУ. Визначається розміром матеріалу порожнього, як правило, 0 ~ 3 мм. Швидкість різання матеріалів, що складаються для машини, часто значно нижча, ніж у звичайної сталі, оскільки збільшення швидкості спричинить сильне знос інструменту, а різні матеріали з нержавіючої сталі мають свою різну оптимальну швидкість різання. Ця оптимальна швидкість різання лише може бути визначена експериментом або консультацією з відповідною інформацією. Під час обробки за допомогою цементованих карбідних інструментів, як правило, рекомендується швидкості різання v = 60 ~ 80 м/хв.
Швидкість подачі F має менший вплив на довговічність інструменту, ніж швидкість різання, але це вплине на розрив мікросхем та видалення мікросхем, тим самим впливає на деформацію та стирання поверхні заготовки та впливає на якість поверхні обробки. Коли шорсткість обробленої поверхні не висока, F повинна бути 0,1 ~ 0,2 мм/r.
Коротше кажучи, для важких для машинних матеріалів зазвичай використовуються нижча швидкість різання та середня кількість подачі.
Виберіть належне охолодження та змащування рідини
Охолоджуюча мастила, що використовується для повороту нержавіючої сталі, повинна мати високу продуктивність охолодження, високу продуктивність змащування та хорошу проникність.
Високі показники охолодження гарантують, що велику кількість різання тепла можна забрати. Нержавіюча сталь має високу жорсткість, і її легко виробляти вбудований край під час різання та погіршення обробленої поверхні. Це вимагає, щоб мастило охолодження має більш високі показники змащування та кращу проникність. Загально застосовувана обробка мастила для охолодження з нержавіючої сталі включає сірчану олію, сірчану соєву олію, гас плюс олеїнову кислоту або рослинну олію, чотирирдовий вуглецевий плюс мінеральна олія, емульсія тощо.
Враховуючи, що сірка має певний корозійний вплив на верстат, рослинна олія (наприклад, соєва олія) легко прикріпити до верстата до верстата і стає несвіжним та погіршено. Автор вибрав суміш чотириручного вуглецю та моторного масла у ваговій співвідношенні 1: 9. Серед них чотириручний вуглець має хорошу проникність і гарну мастило моторного масла. Випробування довели, що ця мастила охолодження підходить для напівфінансування та обробки процесів деталей з нержавіючої сталі з невеликими вимогами до шорсткості поверхні, і особливо підходить для повороту обробки деталей мартенситної нержавіючої сталі.